Thought I'd stick my nose in again. Not sure if you have access to machine tools like lathes and milling machines. My last suggestion assumed you did, although you could make that mounting plate on a bandsaw if you had to.
When I look at your headlight cutout, it scream for a mechanical mounting system to me. I would suggest that you consider an aluminum "socket" for lack of a better term. Machine the socket to hold the LED assemble with screws. Just drill and tap. Aluminum is also a great heat sink.
Then for attachment to the headlight, you could use a bayonet lock arrangement with set screws. The socket would have ears made by machining a groove that matches the ID of your cutout and then machining away 90 deg segments 180 deg opposed. It will leave you two lugs, similar to a cannon breech locking arrangement. On the back side of the groove, and behind the lugs, drill and tap holes that line up with the outer edges of the lugs. These are your locking screws. You can cut away the material to form the lugs with a file, Dremel or if you have one, milling machine and rotary collet head or table.
Now cut out mating cutouts in the headlight opening to allow the lugs to pass thru. You insert the socket and twist 90 degrees and then tighten the 4 screws to secure. You could put a rubber gasket at the back of the groove to make it a nice snug and rattle resistant fit.
The aluminum socket can be made as long as it will fit in the headlight bucket and then cut fins into it on the lathe to give you an excellent heat sink.
If you don't like that idea, then consider making your socket from a spring finger socket. These are the sockets with radial leaf spring finger all around that snap into a hole. They are used for dash light on old cars and instruments on bikes. If you find a supplier, they come in various sizes. Another source would be to just use a similar finger style plug used to plug knock-out holes in electrical boxes. They are a common hardware store item. You may have to adjust your hole size a bit, but you can do that with a Dremel and a stone or a half round file and some patience.
I don't like the epoxy because heat makes epoxy melt or sag. Most of the epoxy putties you buy like JB Weld are probably polyester and soften with heat. If the LEDs get as hot as you say, it will probably melt your epoxy. Only way to know is to do a test.
That's my butting into your project contribution for today. When you get this all worked out, at least electrically and demonstrate that it works and holds up over time, I'm thinking of making a few of these for my Hondas. So, keep up the good work!!
regards,
Rob
LED Headlight Bulb
-
- honda305.com Member
- Posts: 178
- Joined: Sat May 15, 2010 2:23 pm
- Location: San Mateo, Ca
Thanks, Rob. I think maybe you assume that I'm going to be making this for resale or even trying to make it look like stock. That's not the case. I don't mind not having a plug. I don't know how hot the LED will get, but I've tested this compound on a speedo pickup bolt that sat right under my RVF exhaust which blues with heat. I'm not saying I won't run into issues, but I did think about it. If I do see some problems, I'll surely do away with epoxy.
Honestly, I don't have great access to machining tools. There's oldschool, then there's noschool. I'm the latter. I'd love to make something like this work as a sale item. After seeing the brightness and actually measuring the energy consumption, I'm convinced it would work quite well. I plan on doing a few good road trips with this bike when it's all finished. These should prove as good tests for my hodgepodge LED headlight and possibly be the jumping off point for a production model, not unlike the one you've described me building!
Thanks for the input, more updates today... hopefully.
P.S.
There are 7 LEDs, together consuming 12W of energy and a max of about 1645lumen. That's 138-ish lumen/watt which is pretty outstanding. Now I don't know the thermal efficiency of this emitter panel, but it honestly can't output THAT much heat. My dad was estimating maybe 1-3W of heat energy. The thing wasn't even warm to the touch after running it for about 2-3 minutes in testing. I'm not disproving your theory, I'm just establishing my cautious belief that the epoxy will hold.
Honestly, I don't have great access to machining tools. There's oldschool, then there's noschool. I'm the latter. I'd love to make something like this work as a sale item. After seeing the brightness and actually measuring the energy consumption, I'm convinced it would work quite well. I plan on doing a few good road trips with this bike when it's all finished. These should prove as good tests for my hodgepodge LED headlight and possibly be the jumping off point for a production model, not unlike the one you've described me building!
Thanks for the input, more updates today... hopefully.
P.S.
There are 7 LEDs, together consuming 12W of energy and a max of about 1645lumen. That's 138-ish lumen/watt which is pretty outstanding. Now I don't know the thermal efficiency of this emitter panel, but it honestly can't output THAT much heat. My dad was estimating maybe 1-3W of heat energy. The thing wasn't even warm to the touch after running it for about 2-3 minutes in testing. I'm not disproving your theory, I'm just establishing my cautious belief that the epoxy will hold.
I know nothing about these LEDs. But when you put that huge copper heat sink on the back of that light housing, I assumed you could fry an egg on the LED light. Warm to the touch is nothing wrt the epoxy.
What I've been wondering about is a point that either Wilf or G-man made in another thread a month or so ago. They said that the entire charging system is designed as a system and from that I get that each piece was selected to work with the others, do the job and not fry the battery in the process. My question is, if you keep taking load out of the system, will that not put the battery at greater risk of overcharging given there is no regulator or zener like they used on vintage Brit bikes?
Wilf, G-man, you want to weigh in on this here. As you see, I do pay attention to and appreciate what you guys say.
regards,
Rob
What I've been wondering about is a point that either Wilf or G-man made in another thread a month or so ago. They said that the entire charging system is designed as a system and from that I get that each piece was selected to work with the others, do the job and not fry the battery in the process. My question is, if you keep taking load out of the system, will that not put the battery at greater risk of overcharging given there is no regulator or zener like they used on vintage Brit bikes?
Wilf, G-man, you want to weigh in on this here. As you see, I do pay attention to and appreciate what you guys say.
regards,
Rob
-
- honda305.com Member
- Posts: 178
- Joined: Sat May 15, 2010 2:23 pm
- Location: San Mateo, Ca
Thanks for the heads up. I actually have installed a regulated rectifier when I upgraded my charging system as well as an AGM battery. I don't foresee too many issues, but you never know. I'll let anyone in on any problems I have.
Today was a good one. I got the emitter, lens, and plate together with some #4 hardware, zinc-oxide grease, and steel epoxy. They went on just fine and I went on to mounting up the headlight case itself. This was pretty simple. A ton of epoxy and some well-placed weight kept the copper in contact with the headlight well enough. I then tested it all together alongside the original incandescent light. It threw probably an equal amount of light in the same place, plus a lot more out to the sides. It did this while using about half the current of the stock light at the same 12.8V. Here is a comparison video:
http://www.youtube.com/watch?v=PYulBN6itio
Unfortunately, the little iPhone camera didn't pickup the blueish light from the LED as well as the yellowish light from the incandescent bulb. You'll have to take my word for it, the LED is very bright at the same point in the beam as the original lamp, but, as I mentioned, spreads the light pretty evenly across a wide angle. Hopefully you can tell a bit better when the light goes out in the video. That LED was lighting the whole room while the incandescent was lighting a 20" spot on the ceiling.
I also checked the heat. I turned on the light, then left for about an hour. I returned and checked the temperatures with an IR thermometer. At the ends of the heat sink I saw temperatures about 48 degrees C (116F) and at the center, directly behind the LED emitter panel, I saw about 58 degrees C (136F). The glass was a pleasant 25C (78F). If you've ever felt your glass after a long ride with the headlight on, you'll know how good 78F is! The room was fairly cool, but there was no airflow, maybe 50F. I'm quite pleased with the results. All those temperatures are well within the limits of the system and I'm sure the surrounds of the bike-mounted headlight case won't add too much extra heat.
I plan on adding a fuse to the system tomorrow, plus a trim pot for setting an acceptable amount of light for the dimmer switch. Some pictures of today's work:


[/i]
Today was a good one. I got the emitter, lens, and plate together with some #4 hardware, zinc-oxide grease, and steel epoxy. They went on just fine and I went on to mounting up the headlight case itself. This was pretty simple. A ton of epoxy and some well-placed weight kept the copper in contact with the headlight well enough. I then tested it all together alongside the original incandescent light. It threw probably an equal amount of light in the same place, plus a lot more out to the sides. It did this while using about half the current of the stock light at the same 12.8V. Here is a comparison video:
http://www.youtube.com/watch?v=PYulBN6itio
Unfortunately, the little iPhone camera didn't pickup the blueish light from the LED as well as the yellowish light from the incandescent bulb. You'll have to take my word for it, the LED is very bright at the same point in the beam as the original lamp, but, as I mentioned, spreads the light pretty evenly across a wide angle. Hopefully you can tell a bit better when the light goes out in the video. That LED was lighting the whole room while the incandescent was lighting a 20" spot on the ceiling.
I also checked the heat. I turned on the light, then left for about an hour. I returned and checked the temperatures with an IR thermometer. At the ends of the heat sink I saw temperatures about 48 degrees C (116F) and at the center, directly behind the LED emitter panel, I saw about 58 degrees C (136F). The glass was a pleasant 25C (78F). If you've ever felt your glass after a long ride with the headlight on, you'll know how good 78F is! The room was fairly cool, but there was no airflow, maybe 50F. I'm quite pleased with the results. All those temperatures are well within the limits of the system and I'm sure the surrounds of the bike-mounted headlight case won't add too much extra heat.
I plan on adding a fuse to the system tomorrow, plus a trim pot for setting an acceptable amount of light for the dimmer switch. Some pictures of today's work:


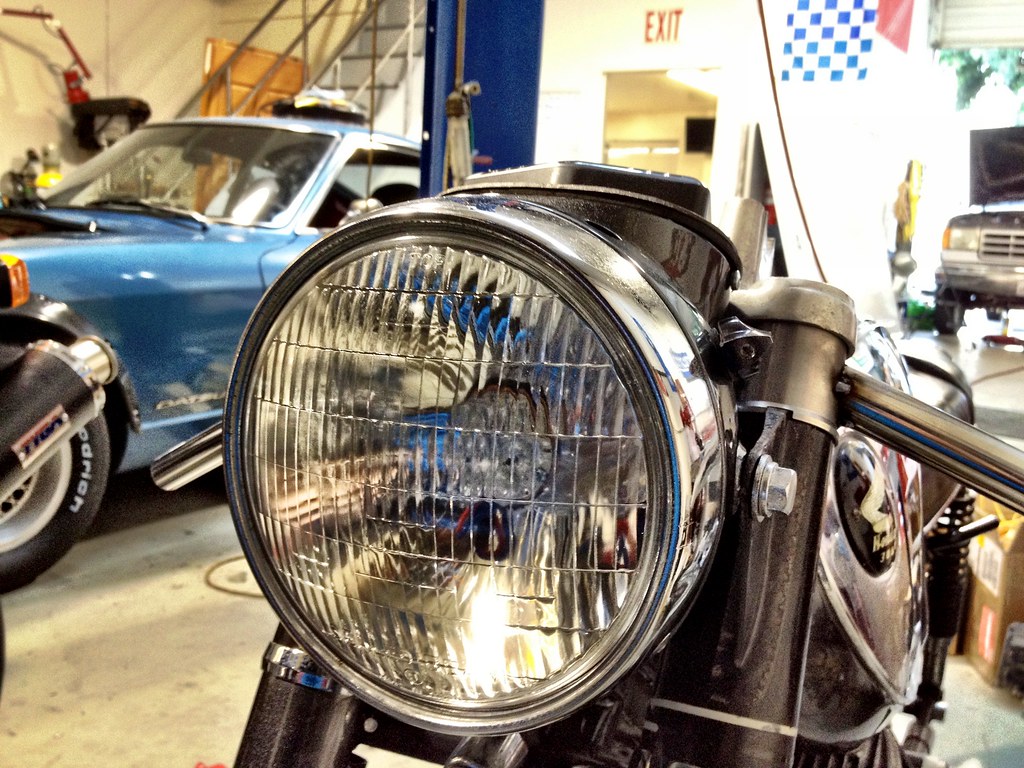
I'm looking forward to how this looks at night on a road situation. Wondering if you will get the same penetration into the darkness with the LED. By that I mean will you light up the road as far ahead as you would with the incandescent bulb? It's really a curiosity thing for me because I will probably never ride any of my Hondas at night unless I get caught somewhere.
regards,
Rob
regards,
Rob
Mbell
Really impressed with the research you are doing here. The light sure looks bright and, judging by the thin wires from your PSU it really efficient. Sensible to put some regulation into your charging system as Rob sensibly points out that the excess power will want to go somewhere.
You should now have plenty to run your fuel injection system!
It would be interesting to shine the two types of light at some kind of test chart on a wall so that the relationship of the reflector and the bulb could be checked out.
The suggestion of turning the LEDs to shine toward the reflector is interesting. An incandescent bulb shines in all directions so the parabolic reflector collects the light and creates a parallel beam pointing forwards.
A really fascinating post
Thanks
G
Really impressed with the research you are doing here. The light sure looks bright and, judging by the thin wires from your PSU it really efficient. Sensible to put some regulation into your charging system as Rob sensibly points out that the excess power will want to go somewhere.
You should now have plenty to run your fuel injection system!
It would be interesting to shine the two types of light at some kind of test chart on a wall so that the relationship of the reflector and the bulb could be checked out.
The suggestion of turning the LEDs to shine toward the reflector is interesting. An incandescent bulb shines in all directions so the parabolic reflector collects the light and creates a parallel beam pointing forwards.
A really fascinating post
Thanks
G
'60 C77 '60 C72 '62 C72 Dream '63 CL72
'61 CB72 '64 CB77 '65 CB160
'66 Matchless 350 '67 CL77
'67 S90 '77 CB400F
'61 CB72 '64 CB77 '65 CB160
'66 Matchless 350 '67 CL77
'67 S90 '77 CB400F
-
- honda305.com Member
- Posts: 178
- Joined: Sat May 15, 2010 2:23 pm
- Location: San Mateo, Ca
Okay, so real quick update. I'm tired, it's late, and I'm up early for work tomorrow.
I got the headlight case all wired. The dimmer switch on the bars now flips between a low and high beam setting in the lamp. In low beam mode it only uses about 3W. That's 1/3 of what the old TAIL light used to use, 12% of what the old low beam used to consume. I won't use it for night riding, I don't think, but it will appease any piggies that would normally rag on me about not having a headlight on while riding during the day.
The high beam is genuinely bright. I don't have a comparison video yet, but below are a few youtube clips I've made to show a bit better what's been going on. Maybe tomorrow night or the next day I'll rig up the old incandescent fixture compared to the new LED deal. I'm impressed and very happy with how it's turned out.
Enjoy:
http://www.youtube.com/watch?v=PYulBN6itio
http://www.youtube.com/watch?v=VlrxBZ3165A
http://www.youtube.com/watch?v=hjUHdeP7XbI
http://www.youtube.com/watch?v=kiaZU2QWm5Y
I got the headlight case all wired. The dimmer switch on the bars now flips between a low and high beam setting in the lamp. In low beam mode it only uses about 3W. That's 1/3 of what the old TAIL light used to use, 12% of what the old low beam used to consume. I won't use it for night riding, I don't think, but it will appease any piggies that would normally rag on me about not having a headlight on while riding during the day.
The high beam is genuinely bright. I don't have a comparison video yet, but below are a few youtube clips I've made to show a bit better what's been going on. Maybe tomorrow night or the next day I'll rig up the old incandescent fixture compared to the new LED deal. I'm impressed and very happy with how it's turned out.
Enjoy:
http://www.youtube.com/watch?v=PYulBN6itio
http://www.youtube.com/watch?v=VlrxBZ3165A
http://www.youtube.com/watch?v=hjUHdeP7XbI
http://www.youtube.com/watch?v=kiaZU2QWm5Y